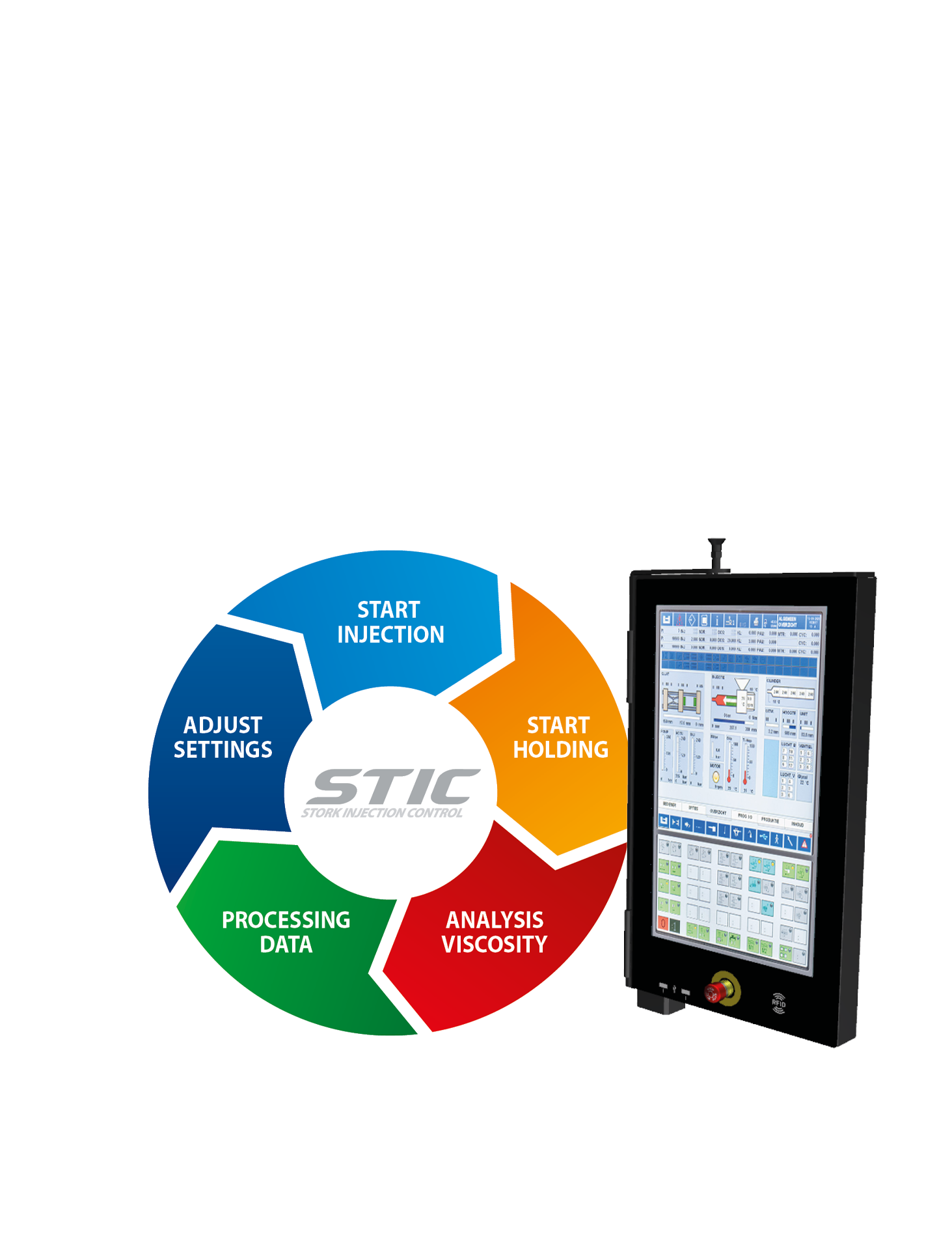
More stable process through STIC
Bato Plastics is a leading manufacturer and supplier of plastic products. Key pillars of the company are maximum quality, fair pricing, and minimal environmental impact. Bato’s customers are primarily growers with whom they work closely to optimize cultivation results.
Bato offers a standard range of horticultural products but also excels in custom solutions. Their products range from thin-walled flower pots to technical components.
Customer: Bato Plastics
Sector: Food
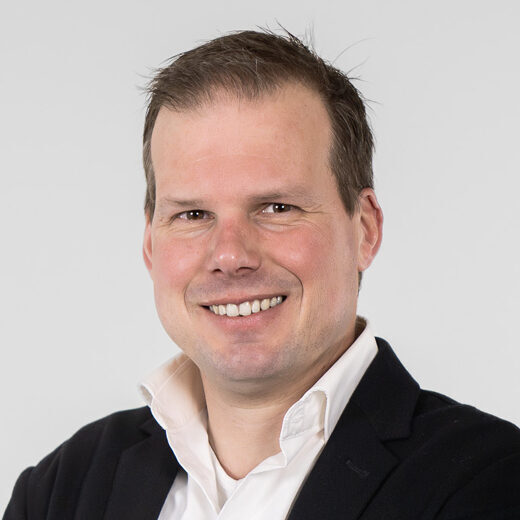
We're happy to help!
Partners with Performance
Stork IMM has been a trusted supplier to Bato for many years, ensuring that its injection moulding machines align perfectly with Bato’s core values.
With its high-performance injection moulding machines, Stork IMM delivers equipment that is both extremely fast and stable in the production process. Additionally, Stork IMM provides rapid service whenever needed.
In the context of sustainable material usage, Bato makes extensive use of regrind material. One of the characteristics of regrind is its inconsistency—material properties tend to fluctuate. A downside of this is the frequent occurrence of defective products: sometimes the product is underfilled and wrinkles, or it’s overfilled and develops flash.
“Products with flash or that are underfilled are very frustrating and disruptive to our production process. Our machines run 24/7, partly unattended, which increases the risk of defects being discovered too late—leading to frustration.”
In the packaging industry, there are already a number of smart solutions that detect and separate defective products. However, these systems are often expensive and the faulty product is already made by the time it is detected.
Stork IMM recognizes this challenge and, in collaboration with several industrial partners, has developed a solution.
The Stork IMM Solution
STIC (STork Injection Control) software is an optional add-on for Stork IMM injection moulding machines. It’s a true Industry 4.0 solution that automatically corrects the injection process in response to MFI (Melt Flow Index) fluctuations. STIC is especially beneficial when producing thin-walled packaging or using recycled materials. Since adjustments are made in real-time during production, this leads to consistently good products and minimal waste.
Implementation and Evaluation
In 2024, Bato began testing STIC. Together with Stork IMM specialists, they first manually walked through the process to identify the necessary corrective actions in response to material fluctuations. The actual STIC testing followed shortly afterward.
The test results were very positive. The products are better and more consistent, resulting in less waste and fewer rejections. This also significantly contributes to customer satisfaction.
In March 2025, Stork IMM evaluated the impact of STIC together with Gregory and Robert from Bato.
Although no quantitative data is available yet, feedback from the production floor has been very positive. Fewer rejections are reported on the machines, less time and specialized knowledge are required to fine-tune the process, and production output has increased.
“For our staff, it’s a relief when an unmanned night shift results in only good products. Rejected items cause frustration and extra work, such as regrinding the rejected materials.”
A more stable process also allows new employees to be trained and deployed more quickly on the machines.
“With the tight labor market and the limited availability of plastics training programs, finding skilled technical personnel is a real challenge. That’s why we train our people in-house—there’s a lot to learn here.”
Bato has now equipped a second machine with STIC software. The return on investment is very short, making it only a matter of time before all machines are equipped with STIC.
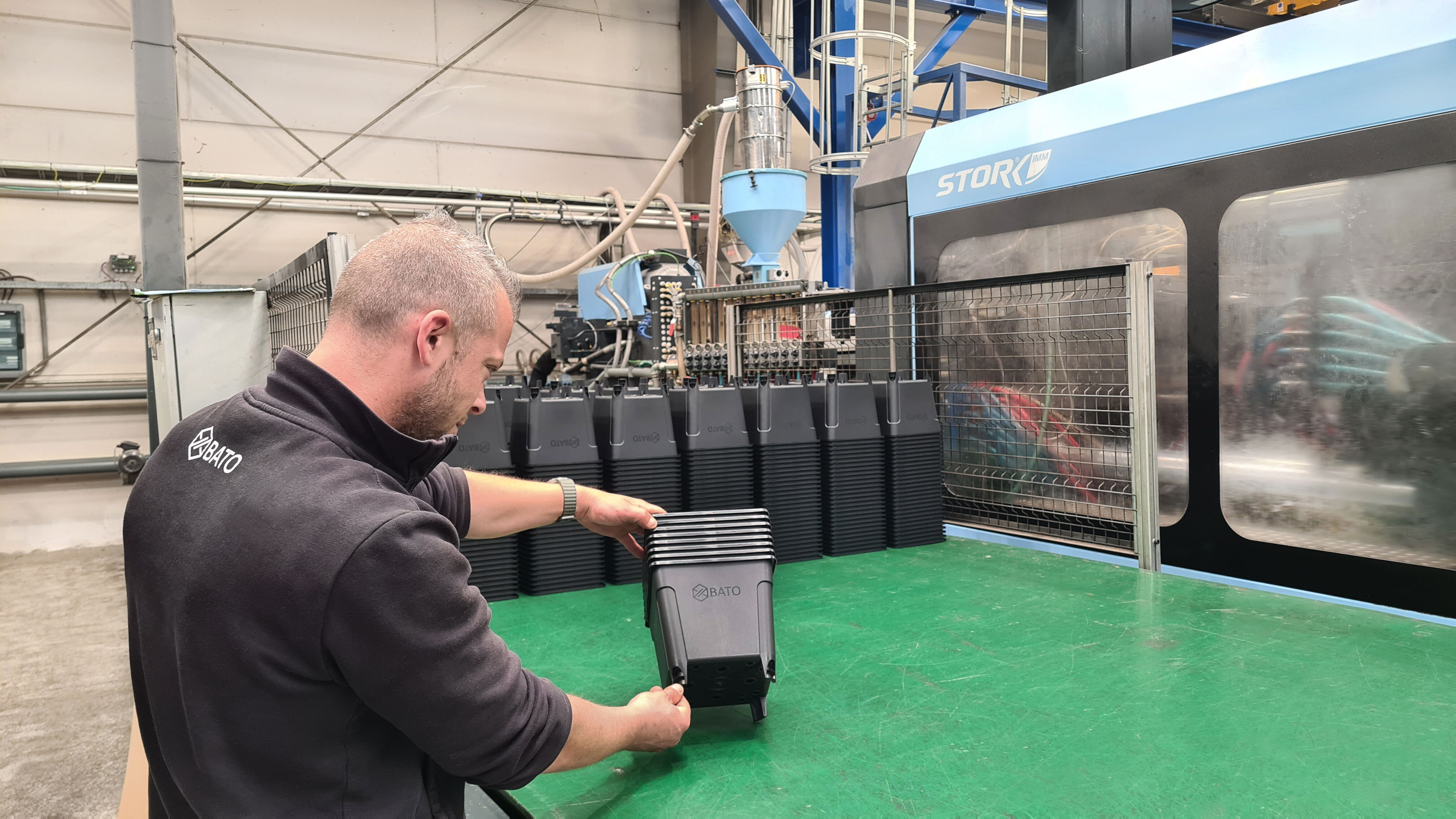
ㅤ
Benefits:
STork Injection Control
More stable production
Increased output and improved product quality with consistent shot weight
Environmentally conscious
Less waste and fewer rejected products
User-friendly operation
Fewer manual interventions required during the production process
customized solutions
Pot-Line
The Pot-Line from Stork IMM is fully focused on high-performance injection moulding machines for the production of flower pots. The various well-developed options are aimed at achieving maximum uptime, minimal energy use, and extremely short cycle times. Our solutions ensure optimal operational protection and homogeneous melting of recyclate.
We also offer options that contribute to an even more stable production process. Perfect for applications involving recyclate or high-cavity moulds—without compromising on dimensional stability or visual appeal.
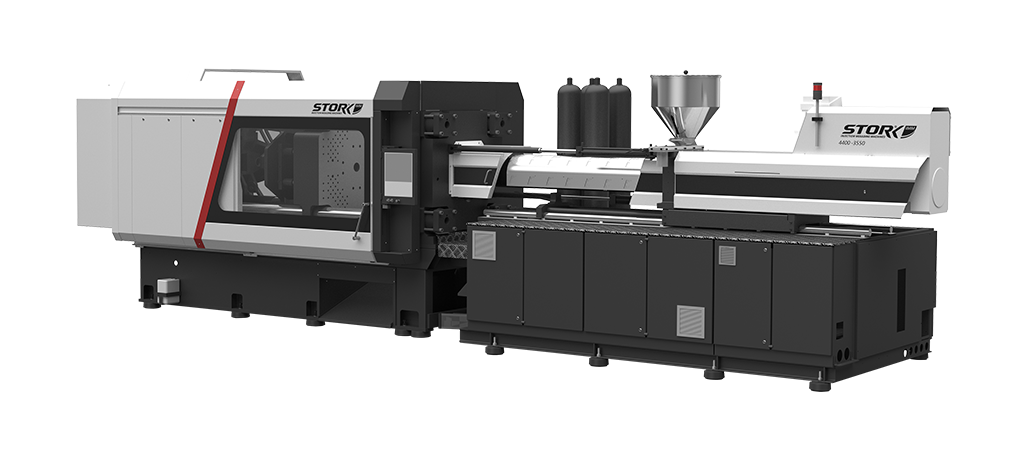