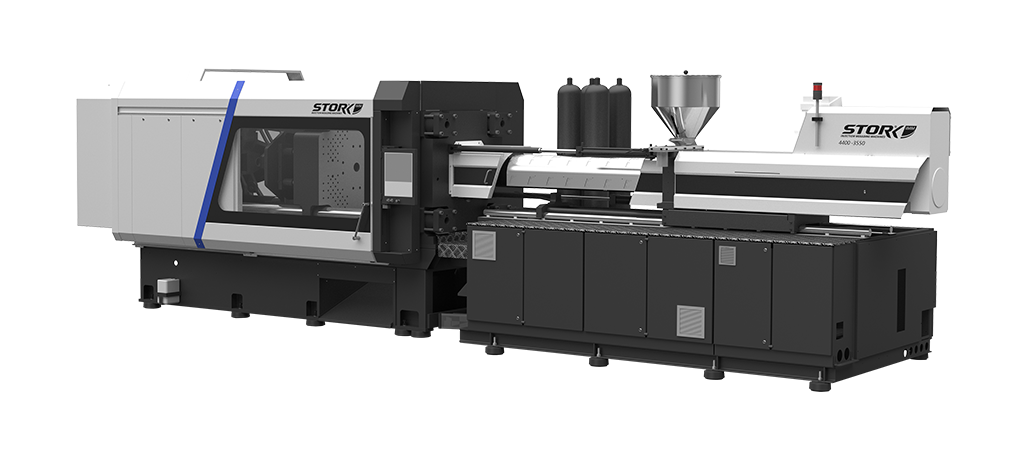
smart customizations
Injection moulding machines for the production of pails and lids
Stork IMM offers a dedicated line of injection moulding machines for efficient pail and lid production.
The machines are tailored for speed, reliability, and consistent product quality.
Flexible configurations ensure the ideal setup for your specific needs.
They support automation, sustainable materials, and perfectly fitting lids.
This makes them the ideal solution for modern, high-performance packaging lines.
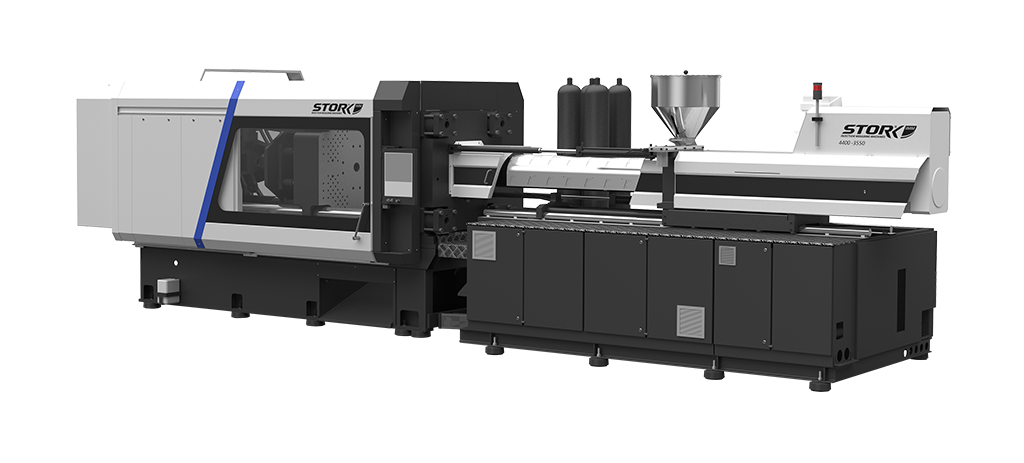
application
Pails and Lids
The production of plastic pails and lids comes with specific and high demands on the injection molding process. Whether you're just starting production or already have years of experience, the focus is on speed, dimensional accuracy, and process stability. Pails must be sturdy, stackable, and impact-resistant, while lids need to close perfectly – a poor fit directly affects quality and customer confidence.
Since pails and lids are often relatively thin-walled with large surface areas, fast and precise injection is critical. At the same time, the process must be highly repeatable – even at high production volumes or when using recycled materials. Consistency in shot weight, wall thickness, and cooling performance is essential to avoid deformation, leakage, or rejects. Production often runs continuously: every second in the cycle counts, and process reliability is key to preventing downtime and waste.
For optimal production, short cycle times, fast mold opening/closing, and reliable demolding are essential. Especially when using multi-cavity molds or integrating automation such as IML, in-mold handles, or robotic take-out, the machine must meet high standards for speed, precision, and accessibility.
A stable machine setup is also crucial – one that is flexible with various materials and can restart production quickly after changeovers or downtime. The result: an efficient and reliable process ready for scaling, innovation, and sustainability.
speed, precision, and stability
Pails and lids
Efficient production of plastic pails and lids demands fast, precise, and stable injection moulding. Key factors include short cycle times, dimensional accuracy, and repeatability—even with recycled materials. Machines must support automation, ensure tight lid fit, and maintain consistent quality at high volumes.
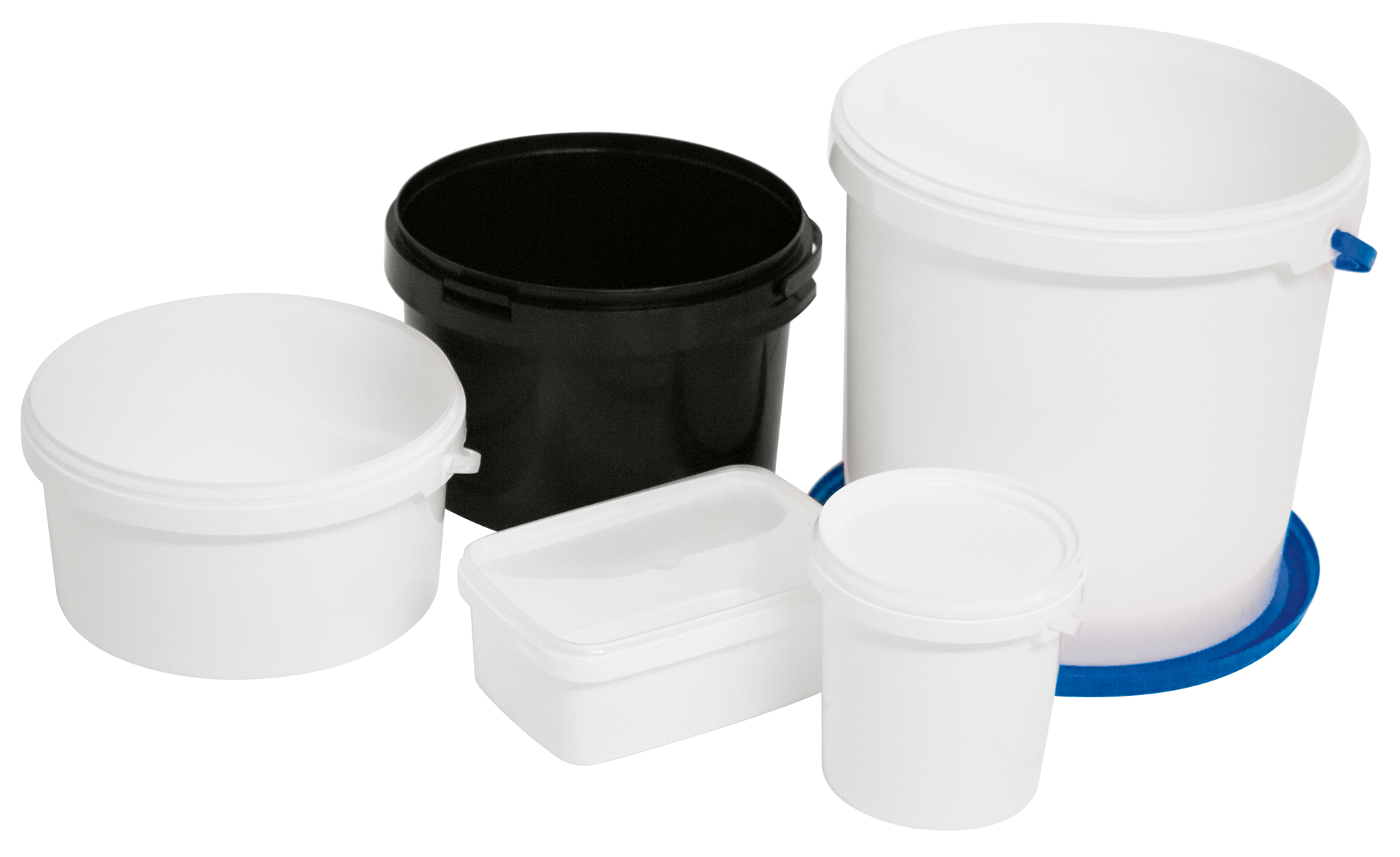
high-performance
Aligned with your production process
Maximum performance, minimal costs, and a sustainable future
Maximum efficiency
Our injection moulding machines are designed for top performance, with maximum uptime and production capacity.
Cost-efficient
Optimize your production process and reduce operational costs with our sustainable and efficient technologies.
Flexible deployment
Our solutions are tailored to your specific production needs, with customizable features for every industry.
Years of experience in machine building
Support and service for maximum productivity
Installed injection moulding machines worldwide
support & service
Our Service and Support
At Stork IMM, we are here to assist you at every stage of the process. From initial installation to ongoing support, we offer complete services to ensure your injection molding machines deliver optimal performance.
our partners
Partners with performance
Quotation
Request your quote now via our form.
We will contact you within a few business days. If you have any questions in the meantime, please call: +31 (0) 74 240 5000.
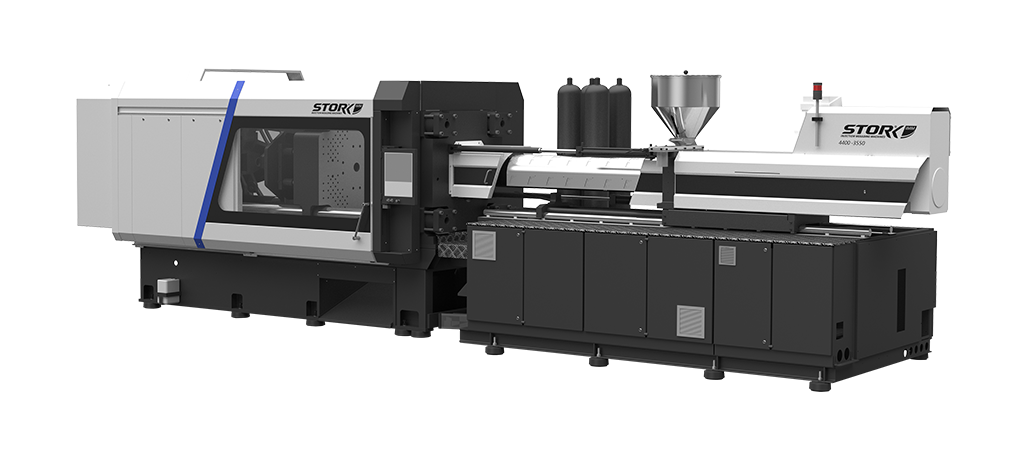
Pail-Line